Hotmelt Moulding
The Low Pressure Molding – also known as low-pressure potting – is a process for encapsulating and protecting electrical and electronic components (such as printed circuit boards or sensors) from environmental influences such as moisture, dust, dirt and vibration.
The technique is also used to mold grommets and strain reliefs, for example for connectors. Low pressure molding mainly uses amorphous thermoplastic polyamides and polyolefins.
They combine a favorable viscosity spectrum with a wide application temperature range of -50 to 150 °C.
Hotmelt process
Hotmelt is a low-pressure overmoulding process in which low thermal stress (short term 200°C) occurs, thus preventing damage to the cable insulation.
The potting material is heated until it is liquid (typically at 180-240 °C). The hot, liquid material is then introduced into a relatively cold mould at very low pressure, typically 5-25 bar.
The material flows gently into the mould cavity and around the electronics to be protected. As soon as the cavity is filled, the preset pressure is generated by the flowing material and the material shrinkage is reduced. At the same time, the cooling process begins as the material hits the outer walls of the moulding cavity. A typical complete moulding cycle takes 10 to 60 seconds.
Direct further processing is then possible without additional cooling or reactivation times.
Hotmelt moulding is perfect for sensitive materials such as circuit boards or relays. The components are mechanically protected and not damaged by the low processing pressure.
Mould making - In-house tool design
Thanks to our in-house mould design, we are very flexible in the area of hotmelt moulding and can implement almost all customer requirements. We design all moulds ourselves and always have the customer’s requirements in mind. Almost any shape and any logo is possible.
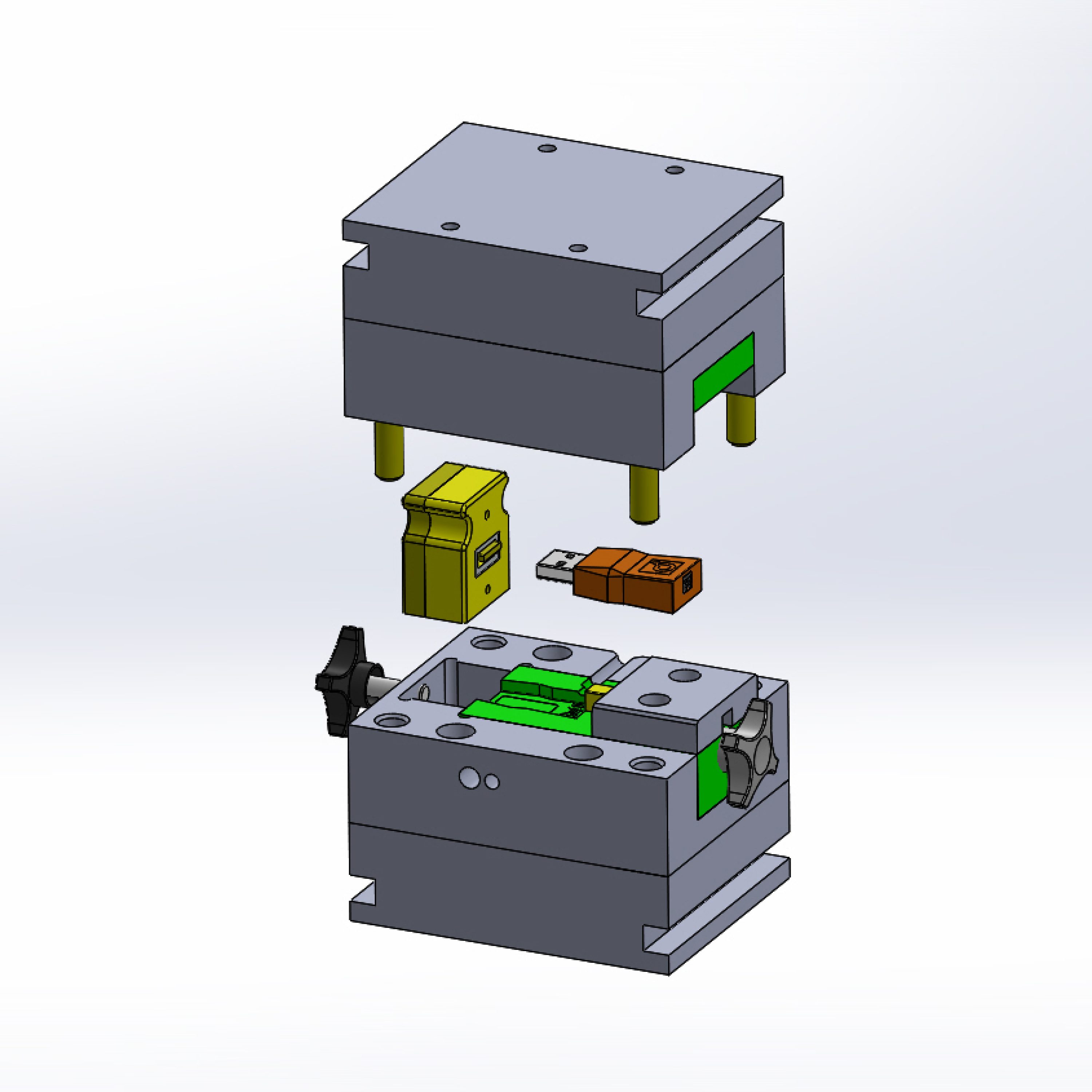
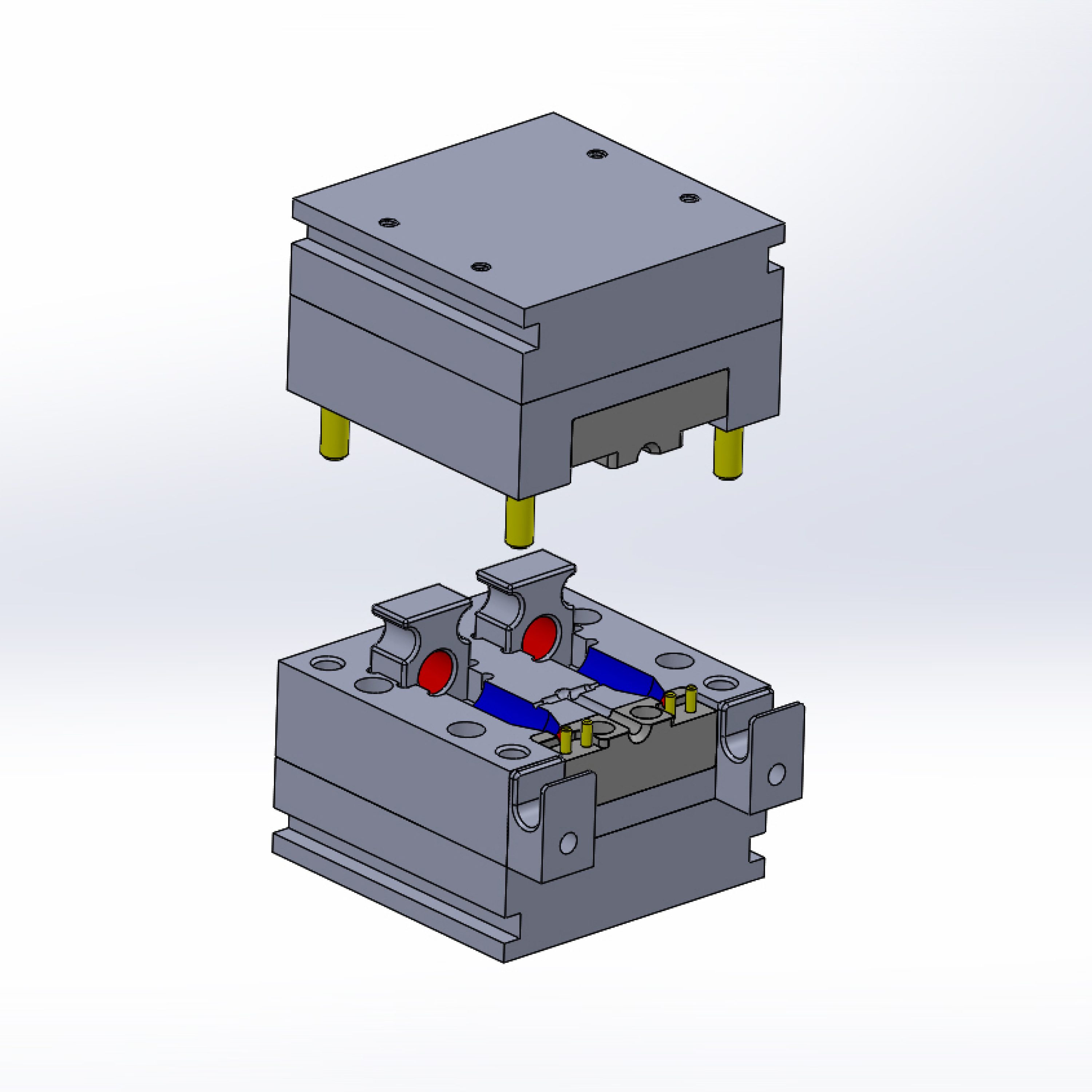
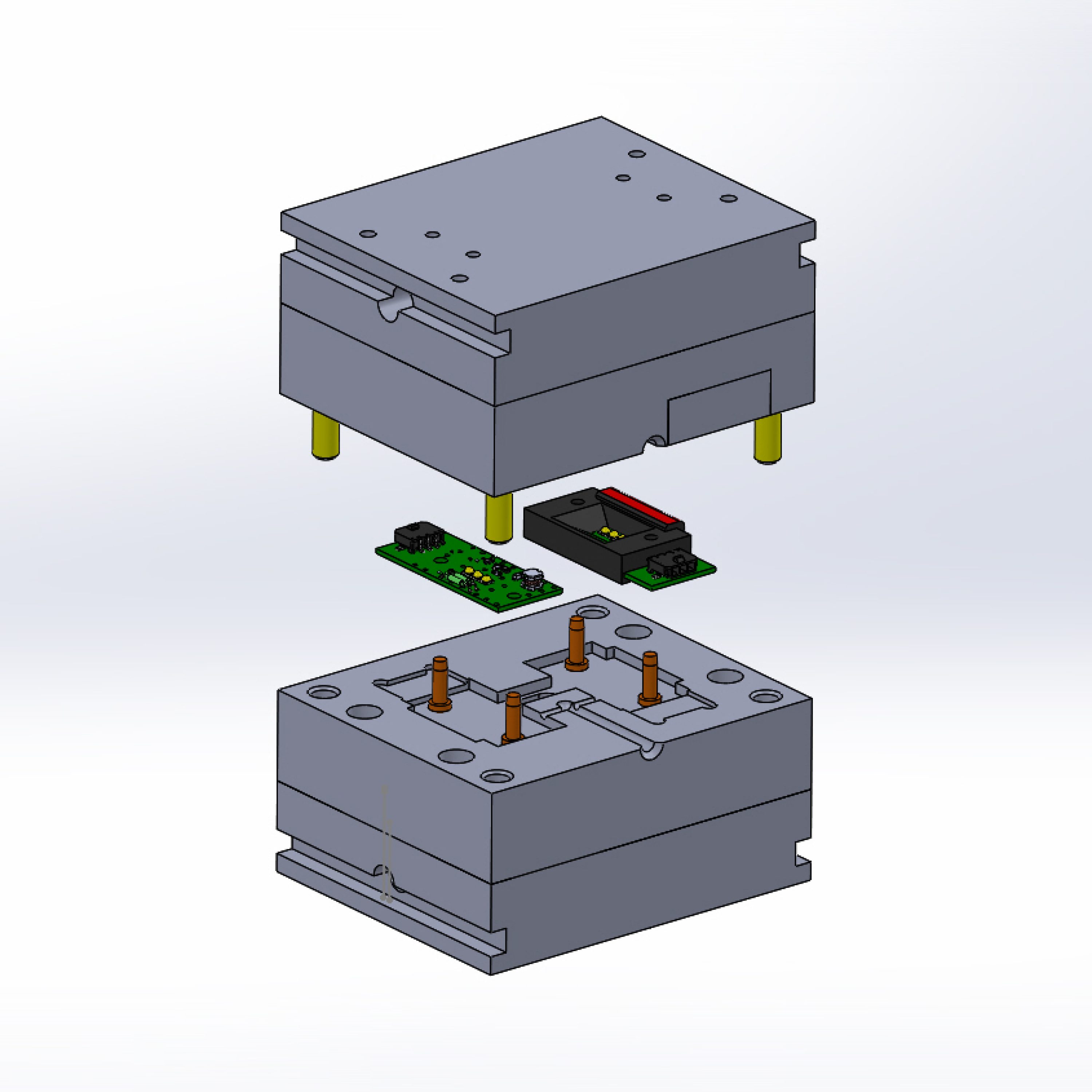
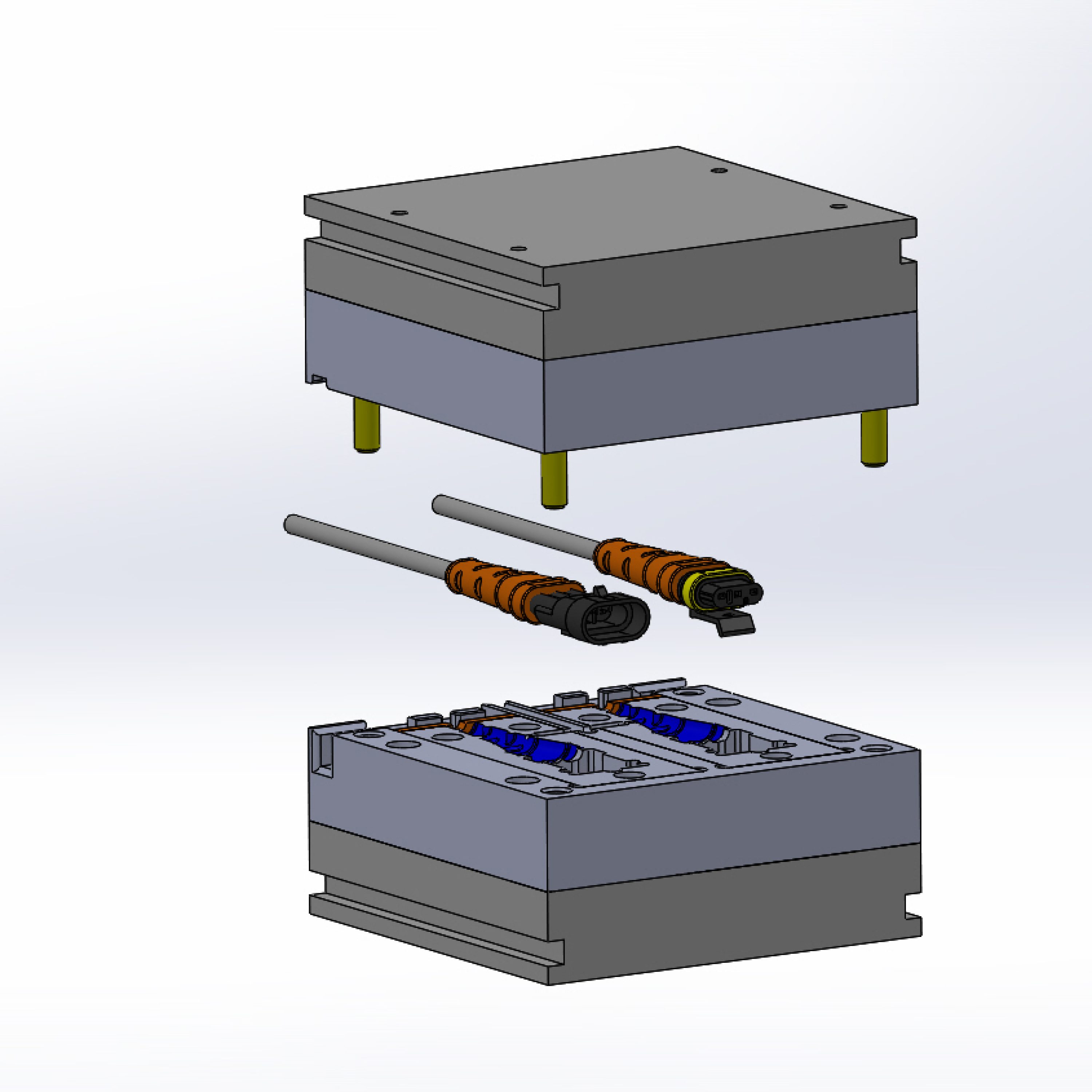
Possible applications
The possible applications in the field of hotmelt moulding are wide-ranging. The process is currently used in our production in the following areas of application:
•Overmoulding of plug connectors
•Overmoulding of ferrites
• Injection moulding of cable grommets
• Injection moulding of strain reliefs
• Injection moulding of holding devices
Hotmelt machine
In our Hungarian production facility ‘PeMaC’, we have two hotmelt machines with highly trained employees.
Thanks to our in-house toolmaking, we can overmould any shape.
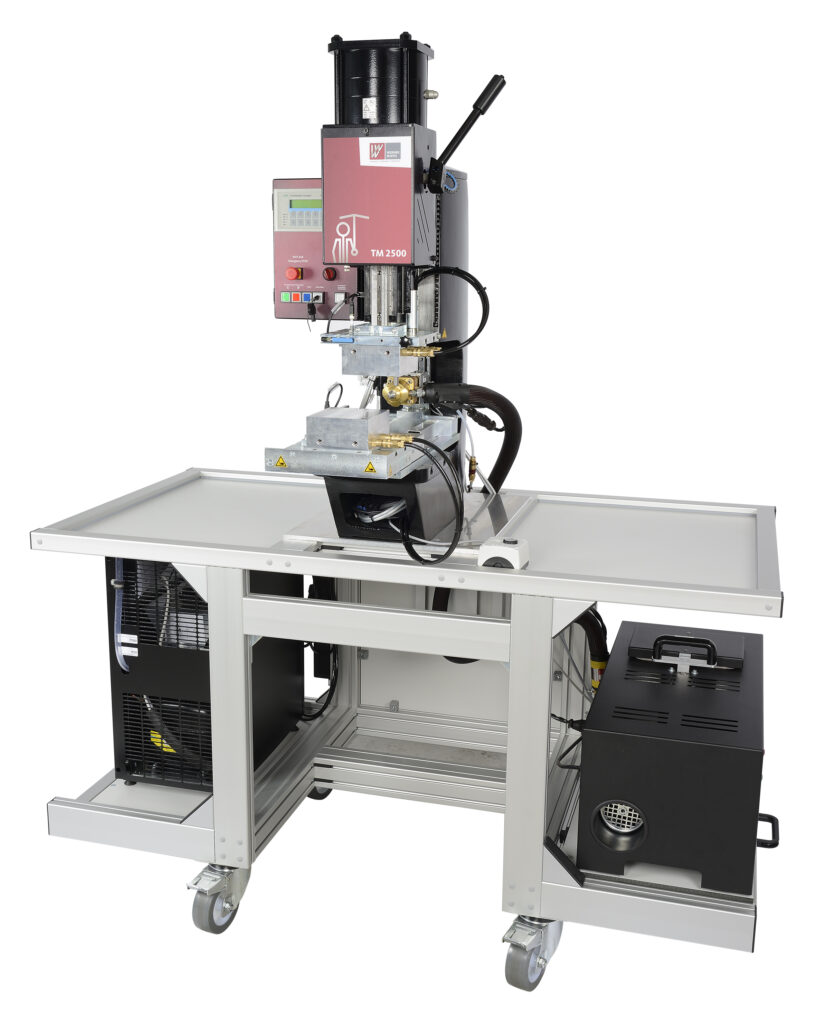